Gummy Manufacturing Equipment Which One Is Best?
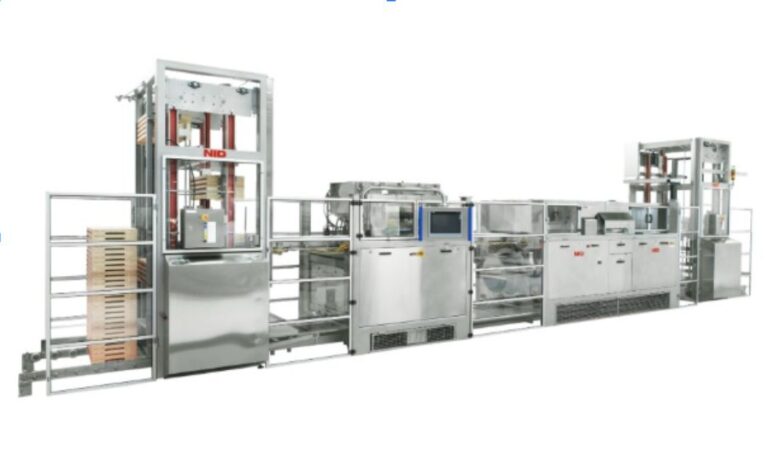
Gummy candies are among the most popular products in the confectionery industry, characterized by their bright colors, chewy texture, and numerous flavors.
Gummies are used as a treat for children or as functional supplements for adults, and they have captured a significant share of the market.
Behind this success lies the importance of reliable gummy manufacturing equipment, which plays a crucial role in ensuring product quality and production efficiency.
If you’re looking to enter the gummy production industry or upgrade your existing setup, the question of “which equipment is best” becomes critical.
This article will give you an in-depth look at the features, comparisons, and factors to consider when choosing gummy manufacturing equipment to meet your production needs.
What Is the Best Gummy Manufacturing Equipment?
The best gummy manufacturing equipment depends on several factors, such as your production scale, budget, and desired level of automation.
Each type of equipment has its strengths and limitations, which can affect production quality and efficiency. Let’s first understand some of the key challenges faced by gummy manufacturers and how selecting the right equipment can address them.
Key Features of the Best Gummy Manufacturing Equipment
To choose the right equipment for your production, here are the key features you should look for in selecting the best gummy manufacturing equipment:
Automation Capabilities
Several of these complex tasks, including cooking, mixing, depositing, and cooling, can be undertaken by automated systems, for which manual intervention is not required. For example, a gummy depositor machine is integral for shaping gummies and ensuring uniform size and precision, which not only enhances efficiency but also ensures consistency across large production batches. This not only speeds up production but also ensures uniformity across batches.
Control over temperature and mixing process
Temperature and consistency in mixing are key to good-quality gummies. High-quality equipment with advanced control systems ensures uniform texture and flavor.
Capacity and Scalability
It doesn’t matter whether you have a small production unit or are one of the large manufacturers; the equipment should match the production capacity but must also be capable of future scalability.
Ease of Maintenance
Machines that are easy to clean and maintain minimize downtime and reduce operational costs.
Food Safety Standards Compliance
Food-grade materials and certifications, such as GMP (Good Manufacturing Practices) and FDA compliance, are essential for safe gummy production.
Gummy Manufacturing Equipment Comparison
Below is a comparison of various types of gummy manufacturing equipment and their suitability for specific production needs:
Machine Type | Key Features | Best For | Estimated Cost Range |
Gelatin Melting Tank | Retains gelatin liquidity | All models | $5,000–$15,000 |
Depositor | Shapes gummies, ensures uniform size | Customizable production | $20,000–$80,000 |
Cooling Tunnel | Ensures proper gummy setting | Medium to large-scale production | $30,000–$100,000 |
Continuous Cooker | High-speed, steady output | Mass production | $50,000–$150,000 |
Batch Cooker | Small batches, precise temperature control | Small-scale production | $10,000–$30,000 |
The choice between these machines is dependent on your production requirements. For example, small manufacturers may use batch cookers and manual depositors, often working with silicone molds for shaping gummies due to their versatility and ease of use. In contrast, large manufacturers require continuous cookers and automated depositing systems to handle higher production volumes efficiently.
Why Automation is a Must for Gummy Production?
Automated equipment is no longer a luxury but a requirement in modern manufacturing. Among the benefits of using automated machines are:
-
Efficiency
Automation significantly raises the speed of production. For instance, an automated line can produce 10,000 gummies per hour, while a manual line can only produce 2,000.
-
Consistency
Automated systems ensure that each gummy is the same size, shape, and texture, minimizing wastage and customer complaints.
-
Labor Savings
Automated machines reduce labor costs by 40%.
-
Scalability
Scalability means that when the demand increases, the automated systems can be scaled up with minimal changes to the production line.
Cost vs. Value: Is Investing in High-End Equipment Worth It
The up-front cost of gummy manufacturing equipment is fairly significant, particularly with automated systems. Long-term value often outweighs this cost. Here is a cost comparison:
Aspect | Manual Equipment | Automated Equipment |
Investment Cost | Low | High |
Production Speed | Moderate | High |
Maintenance Costs | High | Low |
Labor Costs | High | Low |
Quality Consistency | Variable | Excellent |
While the machine sounds inexpensive at first, it usually costs much more to operate later. Automated systems, on the other hand, have consistent output, which saves a lot of money in the long run.
Common Problems Manufacturers Face
-
Inconsistent Quality
Uniformity in size, texture, and flavor is very critical in gummy production. Poor-quality equipment will always produce poor quality.
-
Low Production Efficiency
Such machines or outdated systems have low efficiency for high production demands, thus increasing operational costs.
-
Maintenance Costs
In many instances, poor quality machinery can only be taken to workshops for repair regularly, thereby causing production downtime.
-
Compliance Issues
This will be equipment that does not meet the industry standard, mainly in food-grade production, and can cause some regulatory issues.
The right equipment can deliver efficiency, consistency, and compliance to these problems.
Gummy Manufacturing Equipment Industry
Some data points for your market understanding:
-
Market Growth
The global gummy candy market is expected to grow at a CAGR of 4.5% annually, reaching $42 billion by 2028.
-
Automation Adoption
More than 60% of gummy manufacturers have shifted to automated production lines.
-
Wastage Reduction
Advanced equipment can reduce raw material wastage by up to 15%.
-
Energy Efficiency
Modern machines consume 30% less energy than older models.
Step-by-Step Guide to Selecting the Right Equipment
Follow these steps to ensure you choose the best gummy manufacturing equipment:
Define Your Production Goals. Assess your production scale and budget.
-
Evaluate Features
Look for features like automation, capacity, and precision control.
-
Consider Vendor Reputation
Research vendors with strong after-sales support and warranties.
-
Request Demonstrations
Test equipment performance before making a purchase.
-
Factor in Energy Efficiency
Choose machines with energy-saving features to reduce operational costs.
Conclusion
Choosing the right gummy manufacturing equipment is a relatively complicated but very crucial decision in terms of production quality and efficiency. To find the best equipment, you need to consider factors such as automation, capacity, and maintenance in its design. High-end machinery may incur a higher initial investment cost, but most of the time, the long-term benefits will outweigh the initial costs, meaning consistency, speed, and lower operational expenses.
The more the gummy market grows, the better it is for you if you have invested in reliable and efficient equipment to ensure your competitiveness in this dynamic industry. Whether you are a small-scale producer or a large manufacturer, the right choice of equipment today will set the road to continued success tomorrow.