Understanding Conveyor Systems: The Hidden Risks and Precautions Every Business Should Know
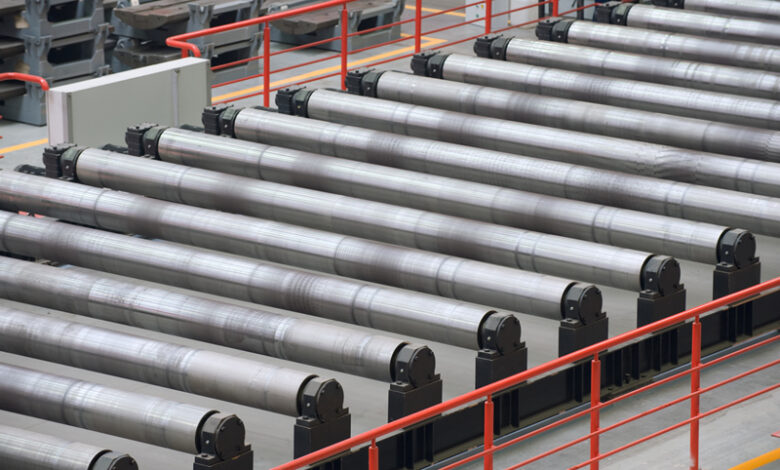
What are Conveyor Systems and how do they work?
The conveyor systems are common to many industries since they form a major part of the material handling systems. However, knowing the operations and the disadvantages of using laser equipment is essential before you put them into your practice. A conveyor system, in its most simple of terms, is responsible for the movement of materials from one location to another with minimum effort on the part of the user with the goal location be a factory floor or a warehouse facility and sometimes both.
There are different types of systems and conveyors for specific systems – industrial tapes for blimps and tons of tea bags or automated robotic systems mounted on conveyor technology for precision movement. The use of the relevant technology can provide numerous advantages when introduced into a certain work activity like the reduction of performance costs within the given activity, the repayment of the investment, the investment into the appropriate system, or the profitability of the integration.
The Common Hazards Associated with Conveyor Systems;
Pinch points are moving parts and areas that can entrap or crush body parts if proper precautions haven’t been taken which is a great occupational danger.
- There must be training for the employees to help them understand these zones and learn how to work around the machines safely and how to use them safely. Also, the dangers from moving parts must not be downgraded; loose clothes and hair could get caught and cause serious injuries.
- Ignoring ergonomic hazards in conveyors can also be costly. Leaving employees at their conveyors for more than a reasonable amount of time increases the risk of RSRIs if appropriate lifting and body use procedures are not taught.
- Hence it is very important for organizations to take safety precautions and give proper education and training for all these risks to be reduced and a safer operating environment for the employees who work with the conveyor systems.
Essential Safety Measures for Operating Conveyor Systems;
Safety protocols, training staff on conveyors, emergency stop mechanisms, and risk assessments for conveyors Operating conveyor systems can considerably improve the productivity of the business however, it is important to make sure that safety comes first to reduce the chances of accidents.
- The first starts with comprehensive training for staff on conveyors, which ought to extend beyond methods of operation to appreciation of the need to observe safety measures.
- A critical point of these protocols is the emergency stop mechanisms which must be installed and routinely tested. These devices need to be positioned in such a way that they are visible and can be actuated with speed during an emergency.
- Also, risk assessments for conveyors should never be an afterthought, they go hand in hand with the installation of the systems. Such evaluations aim at eliminating threats of accidents occurring in the workplace.
If all these precautions are observed, organizations can maintain the effectiveness of their conveyor systems while at the same time improving the safety of employees in the workplace.
The Importance of Regular Maintenance and Inspections of Conveyor Systems;
Periodic maintenance as well as the inspection of conveyor systems is not only ever useful but a necessity in averting undesirable situations in the organization or the factory as well as the efficiency at which the business operates. These essential processes if overlooked can cause problems that are quite bigger than you would expect such as the chances of incurring breakdowns that would be very expensive and also hazards in the workplace.
Inspections of the conveying system on a consistent basis should also be practised to verify that all parts are working correctly. In this regard, some repairs are necessary to avert further damage to the entire system. Failure to recognize and deal with these signs of deterioration, on the other hand, may result in unforeseen downtimes which are undesirable as they will interfere with output and hence profits.
This includes arranging for periodic inspections, maintaining effective inspection report forms, and dealing with recognized problems promptly. In ensuring that these practices are of paramount importance, not only do you shield your investment but also provide a safe work environment for your workers.
How to Choose the Right Conveyor System with Minimum Risk?
Selecting the most suitable conveyor system can deliver enormous benefits to your operational processes, however, it can also be a huge risk if certain precautions are not taken. When selecting conveyor systems safely, one of the best approaches would to be complete a risk assessment during the entire selection process. This means assessing the risk for each type of conveyor system which is available depending on the needs of your business operations.
Now the most pertinent question is if you wish to have standard and custom-made conveyors. Of course, customized systems do have their allure, as bespoke tailor makes them for a specific purpose, but it can actually increase risks and other hassles such as costs and wait time. Whereas, standard conveyors can be reliant and effective, however, they may not have the versatility for More specialized roles. It is necessary to consider these factors before you arrive at a conclusion. Consult people from multiple departments to understand the real risks and operational needs.
Conclusion:
To conclude, conveyor systems can be very useful as they can improve the performance of numerous operations, but safety must always be given priority while installing such equipment. If safety measures are not taken, there can be dangerous accidents that put the welfare of human resources at risk and disturb the operations making huge expenditures in the process.
Risk factors introduced by the equipment should be fully assessed before the conveyor system is fitted for sustained operations. Proper training of all employees on safe work practices and emergency response should be emphasized. The systems’ utilization should be accompanied by regular maintenance checks to avoid equipment malfunction.