The Ultimate Guide to Storing Cleaning Equipment Safely and Effectively
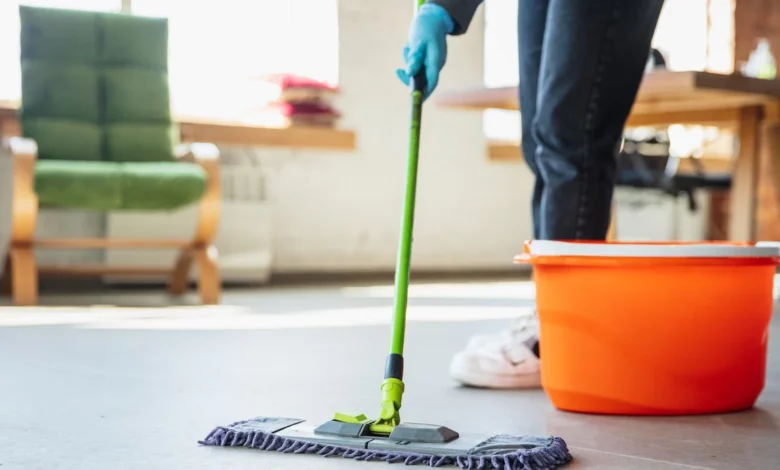
On a busy construction site, cleaning equipment often gets forgotten. Everyone thinks about big machines, heavy tools, and protective gear. But the simple mop, bucket or broom left lying around can cause just as much trouble.
Poor storage of cleaning equipment leads to slips, trips, and even damage to expensive materials. It wastes time, creates hazards, and makes sites look messy and unprofessional. Site owners have a duty to keep working environments safe. That includes making sure cleaning gear is stored properly and used the right way.
This guide looks at why proper storage matters, how to set it up, and how to keep it working day after day.
Why Proper Storage of Cleaning Equipment Matters on Construction Sites
Cleaning equipment is used every day. But it is easy to overlook when it comes to site safety.
A wet mop left blocking a walkway can cause just as serious an accident as a loose cable. Buckets, vacuums and cleaning carts take up space, and if they are not put away properly, they become trip hazards.
Poorly stored equipment also gets damaged faster. Replacing gear costs money and repairs cause delays. Small bits of disorganisation quickly add up to bigger problems across the site.
Proper storage is not about being tidy for the sake of it. It keeps workers safe, protects equipment, and helps keep the site compliant with health and safety regulations.
Site owners who take cleaning seriously send a clear message that every part of site safety matters, not just the obvious risks.
Basic Principles of Safe Cleaning Equipment Storage
A good storage area is simple, tidy and easy to use. It needs to be dry and well-ventilated.
Wet mops and cloths left in sealed cupboards quickly grow mould and bacteria, making cleaning harder instead of easier. Storage areas should be separate from food areas, welfare facilities, and walkways wherever possible.
Cleaning gear should not clutter corridors, block fire exits, or get in the way of workers moving around the site. Equipment must be easy to find and easy to put away.
Racks, hooks, and clear shelves help. Staff should know exactly where each item belongs. The easier it is to use the storage properly, the more likely it is that staff will stick to good habits.
Setting Up a Dedicated Cleaning Storage Area
Every construction site needs a proper place for cleaning gear. Dumping brooms and buckets behind a site cabin is not enough.
Choose a location that is close enough for easy access but not right in the middle of high-traffic areas. It should be dry, have good lighting, and be big enough to fit all the equipment without it being piled up.
Use racks for mops and brooms, shelves for smaller items, and secure cupboards for any chemicals. Clear labelling helps everyone know where things go.
Good cleaning equipment storage protects staff, keeps sites tidy, and helps meet health and safety duties under UK law. Getting it right from the start saves a lot of headaches later.
Organising Equipment for Maximum Safety and Efficiency
A well-organised storage space saves time and cuts risks. Keep similar items together.
Mops and brooms go on racks, buckets and cleaning cloths on shelves, and machines like vacuums need their own safe, dry spaces. Cleaning chemicals must always be kept separate.
They should be locked away if possible, clearly labelled, and never stored above head height. PPE like gloves and goggles should be easy to grab nearby, not hidden away.
That way, staff are more likely to use it properly. Good organisation means staff spend less time searching for gear and more time getting jobs done safely.
Maintaining Storage Areas: Inspections and Accountability
A good system only works if it is maintained. Storage areas need daily tidying.
No dumping wet mops on the floor. No stacking buckets unsafely. Weekly inspections help too.
Check for leaks, broken equipment, missing labels or new hazards. It helps to make one person responsible for the area.
Not to blame them when things go wrong, but to keep a simple routine in place. Accountability keeps standards high and shows that site safety applies to every corner of the project.
Managing Risks from Cleaning Chemicals
Some cleaning products are hazardous. They need extra care.
Under the COSHH Regulations 2002, cleaning chemicals must be stored safely. That means locked cupboards, good ventilation, and proper labelling.
Staff must know how to handle chemicals correctly. No mixing substances. No using chemicals from unlabelled bottles.
Spill kits should be nearby. So, there should be simple instructions for what to do if an accident happens. Keeping chemicals safe protects staff health and avoids regulatory trouble.
Training Workers on Cleaning Equipment Safety
It is easy to assume everyone knows how to handle a mop or bucket. But small mistakes cause big accidents.
Site inductions should include cleaning equipment rules. Toolbox talks can refresh them as projects move along.
Posters in the cleaning area help too. Short, simple reminders about safe storage and correct PPE use keep good habits fresh.
Training does not need to be long or complicated. It just needs to be clear and consistent.
Best Practices for Continuous Improvement
Site conditions change. Storage needs change too.
Review systems regularly, especially when new phases of work start. A cleaning cupboard that worked fine in the early build might not suit later stages.
Ask workers for feedback. They are the ones using the storage every day. They will spot problems early if given the chance.
Link cleaning equipment checks into wider site inspections. It keeps small safety practices connected to bigger ones.
Continuous improvement keeps standards rising, not slipping.
Wrapping Up
Storing cleaning equipment safely and effectively is about more than tidiness.
It protects workers from slips, trips and chemical risks. It keeps tools and gear in good condition. It helps sites run more smoothly.
Construction site owners who invest in good cleaning equipment and storage systems set the tone for better safety across the whole project.
A clean, organised site is a safer, stronger site — and it shows pride in the work being done.