Boost Your Production: Benefits of Using CNC Bending Machines
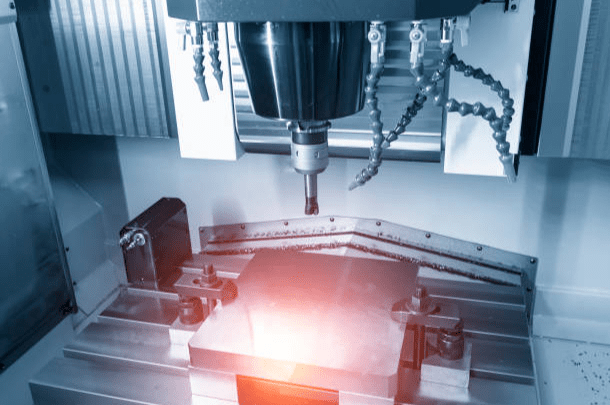
In the realm of modern manufacturing, efficiency, precision, and consistency are key drivers of success. As industries continue to evolve, the need for advanced machinery that can meet these demands grows.
One such innovation that has revolutionized the manufacturing landscape is the Computer Numerical Control (CNC) bending machine. This article explores the myriad benefits of using CNC bending machines in production processes, highlighting how they enhance productivity, ensure precision, and offer a competitive edge in various industries.
Understanding CNC Bending Machines
What Are CNC Bending Machines?
CNC bending machines are automated devices used to bend materials, typically metal sheets or tubes, into specific shapes. These machines are controlled by computer software, which precisely guides the bending process according to pre-programmed instructions.
By leveraging the power of automation and digital control, CNC bending machines offer manufacturers a reliable means to streamline production processes, minimize errors, and optimize output. The CNC technology ensures that each bend is accurate, consistent, and repeatable, making these machines invaluable in high-volume production settings.
How Do CNC Bending Machines Work?
CNC bending machines operate through a combination of mechanical force and software control. The process involves the following steps:
- Design Input: Engineers create a digital design of the desired shape using CAD (Computer-Aided Design) software.
- Programming: The design is converted into a CNC program that dictates the machine’s movements and bending sequences.
- Setup: The material is loaded onto the machine, and the necessary tools are positioned.
- Bending: The machine executes the programmed instructions, bending the material precisely as specified.
- Quality Check: The finished product is inspected for accuracy and quality.
Advantages of Using CNC Bending Machines
Enhanced Precision and Accuracy
One of the most significant benefits of CNC bending machines is their ability to produce highly precise and accurate bends. Traditional bending methods often rely on manual labor, which can lead to inconsistencies and errors. In contrast, CNC machines follow exact specifications, ensuring each bend is identical to the design.
Consistency in Production
The precision of CNC bending machines translates to consistency in production. This is crucial for industries where uniformity is essential, such as automotive, aerospace, and electronics manufacturing. Consistent parts lead to better assembly processes, reduced waste, and higher-quality end products.
Increased Productivity and Efficiency
CNC bending machines significantly boost production efficiency. Their automated nature allows for continuous operation with minimal human intervention. This leads to faster production cycles and higher output rates compared to manual bending processes.
Reduced Setup Time
Setting up a CNC bending machine is quicker and more straightforward than traditional bending methods. Once the machine is programmed, it can switch between different bending tasks with minimal downtime. This flexibility is particularly advantageous for manufacturers handling multiple projects or custom orders.
Cost-Effectiveness
While the initial investment in CNC bending machines can be substantial, the long-term cost savings are considerable. The efficiency, precision, and reduced labor costs associated with these machines lead to a lower cost per unit of production.
Minimized Material Waste
The accuracy of CNC bending machines minimizes material waste, which is a significant cost-saving factor. Precise bends mean fewer errors and less scrap material, contributing to overall cost reduction.
Versatility and Flexibility
CNC bending machines are highly versatile, capable of handling a wide range of materials and thicknesses. They can produce complex bends and intricate shapes that would be challenging or impossible to achieve with manual methods.
Adaptability to Different Industries
The versatility of CNC bending machines makes them suitable for various industries, including automotive, aerospace, construction, and electronics. They can be programmed to create parts for different applications, from simple brackets to complex structural components.
Improved Safety
Automation in CNC bending machines enhances workplace safety. The reduced need for manual intervention means fewer opportunities for accidents and injuries. Safety features, such as automatic shut-offs and protective barriers, further protect operators from potential hazards.
High-Quality Output
The combination of precision, consistency, and efficiency in CNC bending machines results in high-quality finished products. This quality is crucial for maintaining customer satisfaction and meeting industry standards.
Applications of CNC Bending Machines
Automotive Industry
In the automotive industry, CNC bending machines are used to produce various parts, including exhaust systems, chassis components, and suspension parts. The precision and consistency of CNC bending are vital for ensuring the performance and safety of these critical components.
Aerospace Industry
The aerospace industry demands high levels of precision and reliability. CNC bending machines are employed to manufacture components such as airframe parts, brackets, and hydraulic lines. Their ability to produce complex shapes with exact specifications is essential for meeting the stringent standards of this industry.
Construction Industry
In construction, CNC bending machines are used to create structural components, metal frameworks, and reinforcement bars. The versatility of these machines allows for the production of custom parts tailored to specific building requirements.
Electronics Industry
The electronics industry utilizes CNC bending machines to manufacture enclosures, brackets, and other metal parts used in electronic devices. The precision of CNC bending ensures that these components fit perfectly and function reliably within electronic assemblies.
Technological Advancements in CNC Bending Machines
Integration with CAD/CAM Systems
The integration of CAD (Computer-Aided Design) and CAM (Computer-Aided Manufacturing) systems with CNC bending machines has streamlined the production process. Engineers can design parts digitally and directly transfer the specifications to the bending machine, reducing the risk of errors and improving efficiency.
Automation and Robotics
The incorporation of automation and robotics into CNC bending machines has further enhanced their capabilities. Automated material handling systems, robotic arms, and advanced sensors enable continuous operation and increased productivity. These advancements also reduce the need for human intervention, minimizing the potential for errors.
Real-Time Monitoring and Feedback
Modern CNC bending machines are equipped with real-time monitoring and feedback systems. These systems track the bending process, detect deviations, and make immediate adjustments to ensure accuracy. This capability improves quality control and reduces the likelihood of defective parts.
Advanced Tooling Options
CNC bending machines now offer a wide range of tooling options, allowing for greater flexibility in bending different materials and thicknesses. Advanced tooling systems enable quick changes between different bending tasks, enhancing the machine’s versatility.
Factors to Consider When Choosing a CNC Bending Machine
Material Compatibility
When selecting a CNC bending machine, it is crucial to consider the types of materials you will be working with. Different machines are designed to handle specific materials and thicknesses. Ensure that the machine you choose is compatible with the materials you intend to bend.
Bending Capacity
The bending capacity of a CNC machine refers to its ability to handle various thicknesses and lengths of materials. Evaluate your production requirements and choose a machine with the appropriate bending capacity to meet your needs.
Software and Control System
The software and control system of a CNC bending machine play a vital role in its performance. Look for machines with user-friendly interfaces, advanced programming capabilities, and compatibility with your existing CAD/CAM systems.
Maintenance and Support
Consider the maintenance requirements and support services provided by the manufacturer. Regular maintenance is essential to keep the machine operating at peak performance. Choose a manufacturer that offers comprehensive support, including training, troubleshooting, and spare parts availability.
Cost and Return on Investment
While the initial cost of a CNC bending machine can be high, it is essential to evaluate the long-term return on investment (ROI). Consider factors such as increased productivity, reduced labor costs, and improved quality when assessing the ROI of the machine.
Conclusion
The adoption of CNC bending machines in manufacturing offers numerous benefits, including enhanced precision, increased productivity, cost-effectiveness, versatility, and improved safety. These machines have become indispensable in various industries, from automotive and aerospace to construction and electronics. As technology continues to advance, CNC bending machines will play a vital role in shaping the future of manufacturing, driving innovation, and ensuring the production of high-quality, customized products. By investing in CNC bending machines, manufacturers can boost their production capabilities, stay competitive, and meet the ever-evolving demands of the market.