Carbon steel pipe welding technology
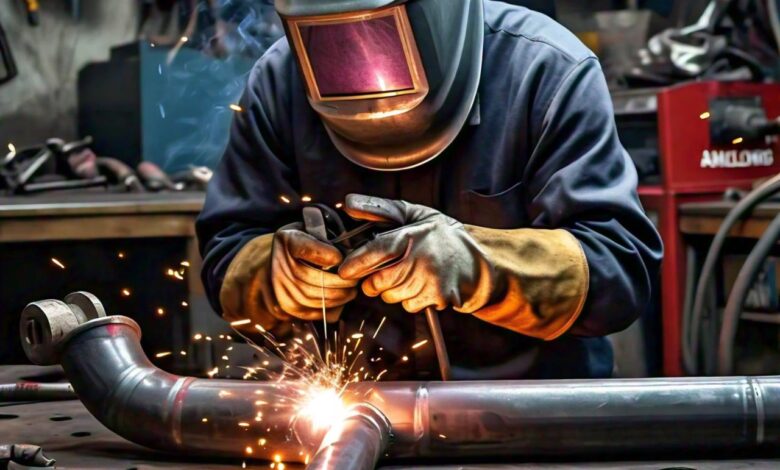
Carbon steel pipes are sturdy, lengthy-lasting, and inexpensive. They are used in many industries, like production and power. Welding those pipes is a unique skill. It needs the proper strategies to make strong, secure welds. This manual explains carbon steel pipe welding, popular methods, and excellent practices. Using first-rate pipes, like HXSCO Carbon Steel Pipe, allows for certain top outcomes for many uses.
Why Choose Carbon Steel for Pipes?
Carbon metal is a combination of iron and carbon. It is powerful, tough, and affordable. Carbon metal resists pressure and handles pressure nicely. It can also withstand high heat, making it ideal for pipes in tough conditions.
Here’s why carbon metallic pipes are so widely used:
Strength: Carbon metal has high tensile energy, which makes it immune to deformation.
Heat Resistance: It holds well below high temperatures, perfect for industries with severe warmness.
Cost-Effectiveness: Compared to different metals, carbon metal is extra low-cost, making it perfect for big-scale applications.
Essential Welding Techniques for Carbon Steel Pipes
Welding carbon metallic pipes requires precision and enjoyment. It also desires an understanding of the proper welding techniques for this fabric. Here are the maximum commonplace welding techniques used for carbon steel pipes:
1. Shielded Metal Arc Welding (SMAW)
Shielded Metal Arc Welding, regularly referred to as stick welding, is one of the most famous strategies for welding carbon metal. It includes using an electrode covered in flux to create a defensive gas defense across the weld.
Advantages of SMAW:
Versatile: SMAW is appropriate for several welding positions, including vertical, horizontal, and overhead.
Cost-Effective: The equipment needed for SMAW is particularly low-cost and smooth to move.
Effective in Harsh Conditions: This technique may be used outdoors, even in windy conditions, because the flux coating protects the weld pool.
Disadvantages of SMAW:
Slower Process: SMAW may be slower compared to different welding methods.
Higher Skill Requirement: More excellent skills are needed to gain steady outcomes.
2. Gas Tungsten Arc Welding (GTAW)
Gas Tungsten Arc Welding GTAW, or TIG welding, uses a tungsten electrode to make the weld. This approach creates excellent welds. However, it also includes slower than other methods.
Advantages of GTAW:
High-Quality Welds: TIG welding produces particularly easy welds with minimal spatter.
Ideal for Thin Materials: It’s well-acceptable for thinner carbon steel pipes.
Precision: Ideal for initiatives requiring meticulous, particular work.
Disadvantages of GTAW:
Slower and Costlier: GTAW is slower and calls for extra luxurious equipment.
Higher Skill Level: TIG welding requires extensive schooling and an excellent grasp of the material.
3. Gas Metal Arc Welding (GMAW)
Gas Metal Arc Welding: GMAW, or MIG welding, is a semi-computerized system wherein a wire electrode feeds through a welding gun, creating an arc that joins the metal portions.
Advantages of GMAW:
High Efficiency: MIG welding is rapid and green, which is ideal for massive projects.
Easy to Learn: GMAW is relatively easy to analyze, making it a popular preference for many welders.
Minimal Cleanup: This process produces much less slag, making publish-weld cleanup faster.
Disadvantages of GMAW:
Less Effective in Outdoor Conditions: The protective gas may be disrupted in windy situations.
Less Precision: Not as particular as TIG welding, which may be a downside for precise work.
4. Flux-Cored Arc Welding (FCAW)
Flux-Cored Arc Welding (FCAW) is similar to MIG welding. However, it uses a tubular wire packed with flux. This approach is practical for welding thick carbon metallic pipes and may be used outside situations.
Advantages of FCAW:
Suitable for Thick Materials: Ideal for welding thick carbon metal pipes.
Suitable for Outdoor Welding: The flux center protects more in windy environments.
High Productivity: FCAW is rapid and green for significant initiatives.
Disadvantages of FCAW:
Slag Formation: FCAW produces slag that calls for cleanup.
Higher Equipment Costs: The wire and equipment are more pricey than other strategies.
Essential Factors in Carbon Steel Pipe Welding
When welding carbon metallic pipes, numerous factors must be considered to ensure solid and reliable welds.
1. Preheating and Post-Weld Heat Treatment
Preheating carbon steel pipes, especially thicker pipes, helps reduce the risk of cracking. The preheating procedure slowly warms the metal, ensuring even warmth distribution. On the other hand, post-weld warmth treatment enables relief of residual pressure from welding, which may enhance the weld’s general durability.
2. Controlling Welding Speed
Welding velocity is important, as it affects both the fineness and power of the weld. Faster welding speeds may also result in insufficient fusion, while slower speeds can cause excessive heat buildup. Maintaining a constant velocity is essential for attaining a balanced weld.
3. Choosing the Right Welding Technique
Choosing the correct welding method is crucial. It relies upon the task’s wishes, like material thickness, environment, and price range. Using the correct technique dramatically affects the final product’s strength and durability. This is proper for HXSCO Carbon Steel Pipe or any top brand.
4. Proper Filler Metal Selection
The filler metal utilized in welding has to suit the properties of the carbon steel pipe to ensure a cohesive bond. Choosing the proper filler steel is essential for weld energy, particularly in high-pressure packages.
Advantages of Using Carbon Steel Pipes in Welding
Carbon metal pipes have many advantages for welding initiatives. They are famous in lots of industries.
High Durability: Carbon metallic’s electricity is ideal for excessive-stress applications like pipelines.
Affordability: Carbon steel is inexpensive than chrome steel. This makes it better for large projects.
Versatility: Carbon steel can withstand numerous welding techniques, permitting flexibility in fabrication and installation.
These advantages make carbon steel an outstanding choice for many business programs. However, it’s vital to work with reliable suppliers. Picking the proper carbon steel maker is critical. Suitable fine materials meet enterprise standards, helping make sturdy, lengthy-lasting welds.
Best Practices for Carbon Steel Pipe Welding
Getting first-rate welds on carbon steel pipes requires careful planning, precision, and the following of high-quality practices.
Proper Preparation: Ensure the pipe surfaces are easy, contaminant-free, and correctly prepped before welding.
Temperature Control: Preheating and maintaining superior temperatures can help save you from cracks and warping within the fabric.
Practice and Skill Development: Welding carbon metal pipes takes skill. Complex strategies, like TIG welding, need more care. Invest in proper training and exercise to develop knowledge of those strategies.
Regular Inspection: Do daily checks and inspections to locate any troubles in the welds. This could be crucial for essential initiatives.
Conclusion
Welding carbon metallic pipes needs exceptional capabilities. It consists of picking the right welding approach, controlling temperature, and adjusting velocity. Whether you use HXSCO Carbon Steel Pipe or some other logo, understanding these steps is fundamental to creating solid and extraordinary welds.
Carbon steel is affordable, strong, and versatile. This makes it ideal for welded pipes in industries like construction, oil and gas, and manufacturing. Choosing the Right Carbon Steel Manufacturer is essential to get high-quality materials. Learning these welding skills and maintaining high standards ensures your projects are safe, reliable, and long-lasting.