The Difference Between Rubber Injection Molding and Plastic Injection Molding
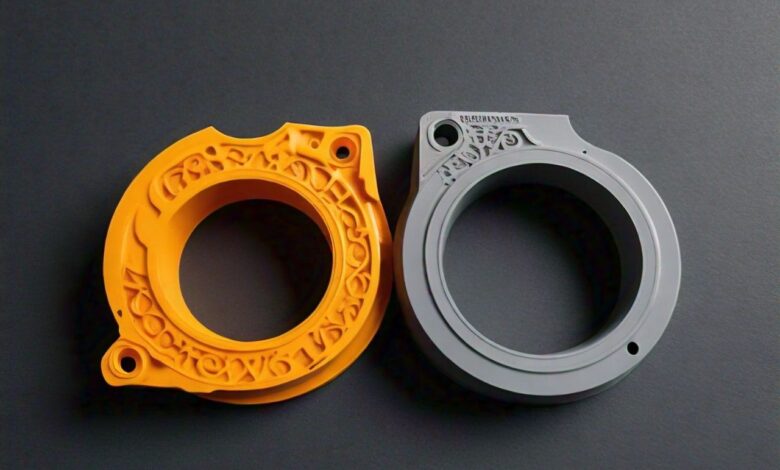
Injection molding is versatile and eco-friendly, but not all types are the same. There are two main types: rubber injection molding and plastic injection molding. They differ in materials, techniques, and applications. Both types are useful, but understanding their differences helps you choose the best option. TASU Rubber Injection Molding Machine provides a reliable choice for rubber-specific injection molding needs.
Understanding the Basics of Injection Molding
Before searching for variations, one can realize what injection molding is and how it works. Injection molding pushes melted fabric into a mold to make components with precise shapes. Once the material cools and hardens, it’s eliminated from the mold as a completed product.
Rubber Injection Molding
Rubber injection molding is a process that pushes rubber into a mold under excessive stress. It is regularly used to make rubber parts like seals, gaskets, O-jewelry, and car elements. Rubber is a special cloth, so it requires a completely unique molding method. This method generally includes curing, or vulcanization, to keep the rubber’s form and properties stable.
Characteristics of Rubber Injection Molding
Material Properties Rubber has unique features. It is flexible, warmth-resistant, and seals well. Rubber injection molding makes use of natural or synthetic rubber. This rubber wishes vulcanization to shape its form and home ultimately.
Vulcanization Process Vulcanization is a crucial step in rubber molding. It links rubber molecules to form a solid shape, helping the rubber preserve its form, flexibility, and energy.
High-Pressure Injection Rubber molding desires higher injection pressures. This is because rubber is thick and difficult to drift. High strain facilitates reaping the favored detail and uniformity in the molded components.
Complex Geometries: Rubber injection molding can make complicated shapes. It is suitable for components that need flexibility and precision, including clinical devices and seals.
Applications of Rubber Injection Molding
Rubber injection molding is ideal for products that need flexibility and power. It additionally works properly for parts that withstand high or low temperatures.
Common packages include:
Automotive Parts: Rubber gaskets, seals, and hoses utilized in vehicles.
Medical Devices: Seals and O-earrings for scientific devices.
Industrial Seals: Gaskets and vibration dampeners for equipment.
Plastic Injection Molding
Plastic injection molding is a common manufacturing technique. It produces many plastic merchandise, from normal objects to complicated industrial elements.
In this procedure, plastic pellets are melted. The melted plastic is injected right into a mold to shape shapes. Unlike rubber, plastic isn’t always vulcanized. It hardens with the aid of cooling.
Characteristics of Plastic Injection Molding
Material Versatility Plastic injection molding uses many styles of thermoplastic materials, each with different properties. Common plastics used in injection molding are ABS, polypropylene, polystyrene, and polycarbonate.
Plastic materials are easier to paint with than rubber. They can be injected at lower pressures, which makes them brilliant for generating many uniform elements with much less wear on molds and machines.
Cooling and Solidification: Plastic injection molding cools the plastic to harden it. Rubber desires vulcanization to harden. The cooling level is crucial for the accuracy and energy of plastic components.
Plastics usually are more inflexible than rubber. This limits their use in flexible regions. However, plastics are robust, long-lasting, and resistant to put on. They are used in lots of packages.
Plastic injection molding is exceptionally flexible and utilized in a variety of industries:
Consumer Goods: Plastic injection molding is used for merchandise like cellphone cases, boxes, and toys.
Automotive Components: Parts such as dashboards, bumpers, and interior trims.
Electronics: Enclosures, connectors, and casings.
Critical Differences Between Rubber and Plastic Injection Molding
Knowing the key differences enables you to pick an excellent approach. This will fit you.
1. Material Properties and Processing
Rubber: Requires vulcanization, making it resilient, flexible, and ideal for sealing programs.
Plastic: It hardens while cooled and is usually rigid, making it proper for structural elements
2. Molding Process
Rubber Injection Molding uses excessive pressure to handle the rubber’s thickness. Curing time is needed for vulcanization.
Plastic Injection Molding: Uses slight stress, focusing on cooling and solidification.
3. Equipment Used
Rubber: Requires specialized machines that withstand high pressures and warmth-resistant molds for vulcanization. The TASU Rubber Injection Molding machine is made to manage rubber materials.
Plastic: Plastic injection molding equipment operates at decreased temperatures and pressures.
4. Product Characteristics
Rubber Parts: Rubber elements are bendy, elastic, and seal well. They are super for absorbing shocks and handling extreme conditions.
Plastic Parts: Plastic components are rigid, strong, and versatile. They are frequently used when durable and lightweight parts are needed.
5. Cost and Production Volume
Rubber Molding costs more due to the high stress and special equipment required. It’s often better suited for smaller manufacturing runs.
Plastic Molding: More powerful for high-volume manufacturing, making it best for heavily produced goods.
Choosing the Right Molding Process
Choosing between rubber and plastic injection molding depends on your undertaking’s needs. Here are a few questions to guide your selection:
What is the product for? Rubber molding is the quality choice if the application requires flexibility, sealing, or warmth resistance.
What is the predicted production volume? Plastic injection molding is cheaper for big manufacturing, while rubber injection molding is regularly better for small runs or unique uses.
What machinery is needed? Rubber molding requires high-pressure machines and heat-resistant molds, while plastic molding uses a regular plastic injection system.
By understanding each approach’s functions, manufacturers can make better selections, which results in more satisfactory merchandise and quicker production.
Conclusion
Rubber and plastic injection molding are essential for making different merchandise. Rubber injection molding is exceptional for flexible elements like seals and gaskets, and plastic injection molding is good for making robust, inflexible parts in large numbers. Machines like the TASU Rubber Injection Molding gadget make unique, wonderful components.
Choosing the proper method depends on the fabric, manufacturing desires, and finances. Knowing the variations allows you to select your product’s quality.