Why Using CNC Turned Parts Pays Off in Small-Batch Runs
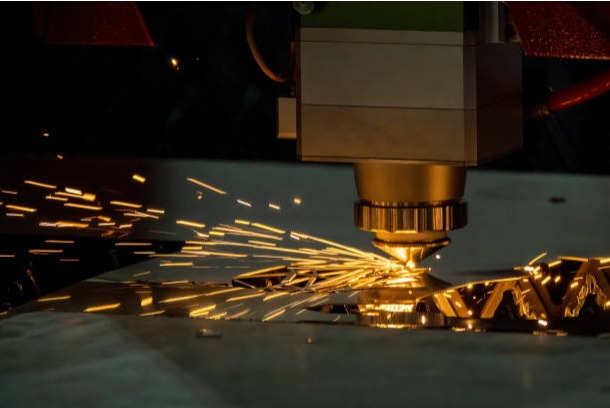
In today’s custom-manufacturing climate, lots of industries-soft-focused on aerospace, robotics, and medical gear-are steering toward small-batch runs rather than big-volume, one-size-fits-all orders. Those fields ask for quick lead times, tight tolerances, and plenty of design wiggle room, yet they want to dodge the heavy cost of a full mass-production line. As those pressures mount, the humble CNC turning part quietly keeps winning favor.
True, CNC milling usually steals the limelight, but turning is what shapes round features like shafts, bushings, and gears with impressive repeatability. For small runs, parts made this way deliver a set of hidden perks that go far beyond the numbers etched on a technical datasheet.
The sections below lay out four reasons to pull CNC turning into your low-volume projects-and why B2B buyers and engineers should keep it high on their shortlist.
Flexibility in Design with No Drop in Accuracy
Perhaps the biggest win with a CNC turning part is how easily it can manage detailed profiles that would eat up time and budget on a shop-floor lathe or manual tool.
CNC turning really shines when you need to make:
- Uniform cylinders or handy conical shapes
- Sharp threads, deep grooves, or tricky undercuts
- Parts that fit together perfectly around a center
- Items that must look good right off the machine
For short runs, this flexibility means you get custom work done exactly the way you pictured it, without losing tight tolerances or steady repeatability. Because it skips the costly, time-draining molds and dies of casting or stamping, CNC turning lets engineers tweak a design today and cut the updated part tomorrow.
Put a CNC turning piece next to a CNC precision machined part in the same program, and you can quickly test hybrid units that are tough on the outside and smart on the inside.
Reduced Setup Time and Faster Prototyping
Set-up, tooling, and fixture work can chew up money fast in any shop. When thousands of pieces roll off a single run, that expense gets diluted. But in small batches, every minute spent fiddling with jigs pushes profits in the wrong direction.
CNC turning is a smart choice for small production runs because:
- Tool paths get programmed once and can be tweaked, not rebuilt, for the next batch.
- Setup is quick thanks to automatic, fast-swap tooling.
- Machines need only a minor calibration each time, if that.
- CAM software spits out prototypes and adjustments in minutes.
These perks slash lead times. A well-set CNC lathe can crank out usable CNC precision parts in hours, not the days or weeks that manual shops require. For fast-moving fields like robotics or automotive R&D, that speed becomes an edge.
Cost-Effective Production Without Sacrificing Quality
People usually think of cutting costs on small runs by trimming scrap or labor. With CNC turning, the biggest bang for your buck comes from holding tight tolerances and steady quality while producing very little waste.
Here is how CNC turning earns its reputation for tight accuracy:
- CNC lathes keep every part in a run nearly identical.
- Real-time sensors catch drift before it starts.
- High first-pass yield cuts back on costly rework.
- Strong clamps and fixtures stop parts from shifting.
These points matter most when failure could leak oil or air. A single bad dimension can ground a plane or an MRI machine.
Parts made this way often need little extra cleanup or touch-up. That keeps the job moving, cuts costs, and helps small shops stay lean.
Superior Material Flexibility for Specialized Needs
Another quiet advantage of CNC turning is its wide appetite for raw stock. Where some methods work only with aluminum or mild steel, turning accepts:
- Titanium
- Inconel
- Brass
- Hardened tool steels
- High-performance plastics like PEEK or Delrin
This freedom lets makers produce items as varied as surgical tools or jet sensors in small batches without special lines.
B2B customers working in tightly regulated or high-spec fields often order small lots made from hard-to-find, exotic alloys. CNC-turning equipment meets both demands: the process cuts those tough materials easily and holds tolerances that drift by only a few microns. When you pair those turned parts with cnc precision machining parts shaped through milling or grinding, one shop can deliver a full suite of components without the hassle of coordinating several suppliers.
Easier Quality Control and Traceability
In small-batch work destined for regulated markets, traceability and quality tests are never optional. Because mass runs justify expensive, all-in inspection robots large volumes bring, low quantities rely on leaner, focused checks that still certify each part.
CNC lathes simplify that job by recording:
- Digital logs of tool paths, spindle speeds, and exact tolerances
- Plug-and-play links to coordinate-measuring machines (CMMs)
- Repeatable setups that turn out every piece the same
- Cycle files saved for every run
Keeping every metric in digital form speeds up getting ISO stamps, CE tags, or any proof that every part meets the rule book. Whether the order lands in a medical lab or on an aerospace line, that built-in data stream from your turning centers cuts paperwork time and builds trust with every signature.
Because the computer can check every move in real time, shops can say yes to new ideas almost immediately. That speed, combined with clear job tracking and a steady chain of approvals, makes CNC turning the go-to partner for B2B clients who want a flexible and reliable process.
Conclusion: CNC Turning Is More Than a Spindle-It’s a Strategy
Today, when many firms run small-batch lines, the humble CNC turning part has taken on a bigger role. It is no longer a simple cut of metal; it is a linchpin in an overall plan for speed, adaptability, and rock-solid quality.
By weaving cnc turning parts and cnc precision machining parts into daily operations, manufacturers can:
- Move prototypes and short runs from sketch to shelf faster
- Hold tight tolerances even on complex shapes
- Shift materials or redesigns without missing a beat
- Offer budget-friendly work with less chance of trouble
- Boost digital records and keep the process in plain sight
For teams wanting a tool that scales, adapts, and never drops the bar on quality, CNC turning is far more than a hidden edge-it is a must-have fixture on the shop floor.