Sustainable Investment Casting Techniques
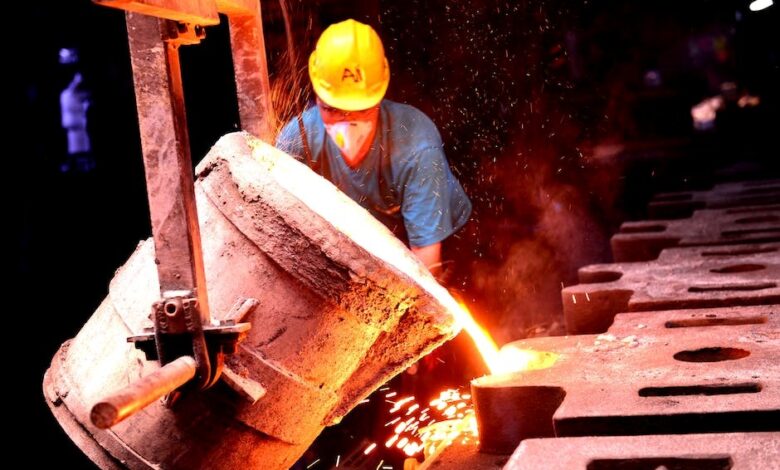
What if you could create high-quality metal parts while also helping the planet? That’s the idea behind sustainable investment casting techniques. This method is being improved to use less energy, create less waste, and rely on more eco-friendly materials-without giving up strength or precision.
In this article, we’ll break down how these greener casting methods work and why more companies are making the switch. If you’re interested in cleaner, smarter ways to produce metal parts, keep reading-you won’t want to miss this.
Reusable Wax Patterns
In sustainable investment casting, reusable wax patterns play an important role in reducing waste. After a casting is completed, the wax can be melted down and recovered for reuse. This process cuts down on the need to produce new wax, which saves both resources and energy.
Reusing wax helps to lower the overall environmental footprint of the casting process. The recovered wax is cleaned and reshaped into new patterns, ready for the next cycle. This approach is not only cost-effective but also helps maintain the consistency and quality of the casts.
Ceramic Shell Optimization
Optimizing ceramic shells in investment casting can lead to significant environmental benefits. Thinner shells reduce the amount of material needed. This lowers waste and costs.
Stronger ceramic materials allow for better mold quality and durability. This means fewer shells are required. This reduces the need for constant production of new ceramic shells, conserving resources. Advanced ceramic technologies also help improve the casting process by offering more precise and efficient mold creation.
Energy-Efficient Melting
Energy-efficient melting is an important technique in sustainable investment casting. By using advanced furnaces, less energy is required to melt materials like stainless steel. These furnaces are designed to minimize heat loss and operate at higher efficiencies.
This means less fuel is needed, which reduces both energy consumption and costs. In stainless steel casting, using energy-efficient methods helps to maintain the quality of the metal while lowering the environmental impact. It also helps to lower the carbon footprint of the casting process.
Sand and Shell Recycling
Recycling sand and shells helps reduce waste in the investment casting process. After a casting is completed, the sand used for molding can be collected and reused. The shells, which are made from ceramic materials, can also be recycled after the casting is done.
By reusing these materials, manufacturers cut down on the need for new raw materials, lowering costs and waste. This process not only saves money but also reduces the environmental impact of producing new sand and shells. Recycling helps keep the process more sustainable while maintaining the quality of the final product.
Cleaner Alloy Practices
Cleaner alloy practices focus on using materials that have less environmental impact. In steel casting, choosing low-carbon alloys reduces harmful emissions. These alloys require less energy to produce and cause fewer pollutants during the melting process.
By using cleaner alloys, manufacturers can create high-quality products while being more eco-friendly. The process also reduces the need for refining, which helps save energy. In addition, cleaner alloys improve the overall sustainability of the casting process.
Explore these Investment Casting Techniques
Sustainable investment casting techniques are becoming essential in reducing environmental impact. These methods focus on using eco-friendly materials and energy-efficient processes.
By improving waste management and reducing emissions, they help protect natural resources.
Looking for more tips and ideas? We’ve got you covered. Check out some of our other posts now.